Problem:
A manufacturer of industrial paint mixers struggled for years with mount durability issues. The customer was using off-the-shelf catalog mounts to isolate the frame of a paint mixer from the vibrating (paint-mixing) sub-frame (Figure 1). The extremely aggressive application required isolators to allow large vibratory displacements (+/- 0.5 inches at 9 to 28 Hz) of the paint mixer sub-frame while minimizing forces transmitted to the frame. Poorly designed mounts led to premature fatigue failure rendering the paint mixer ineffective and resulting in significant warranty claims
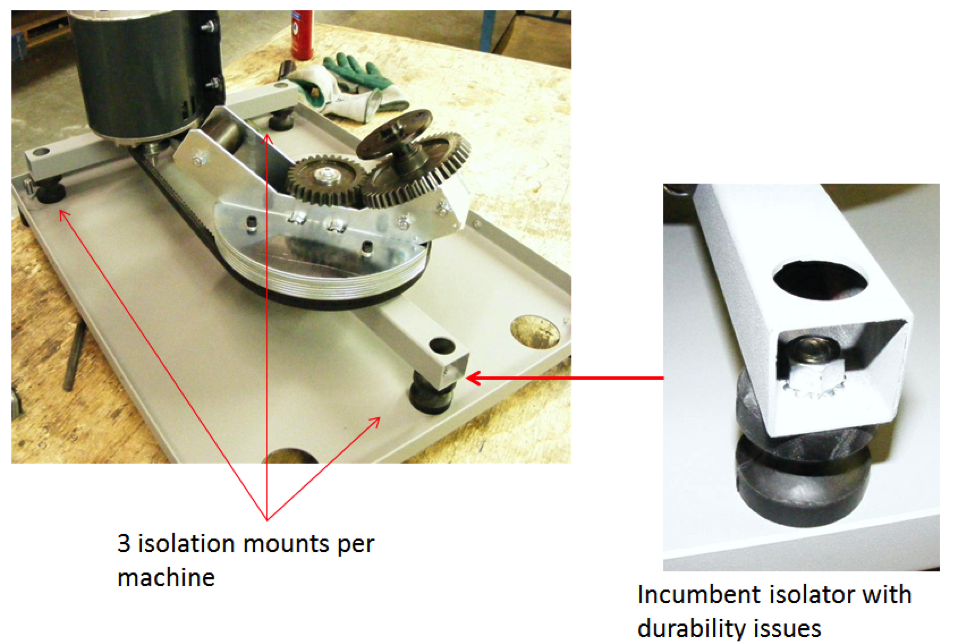
Figure 1 – Location of isolation mounts for aggressive paint mixer application.
Approach:
An understanding of vibratory forces, static loads and durability requirements was necessary to design a custom isolator. Engineering software tools such as hyperelastic finite element analysis (FEA) were used to design and optimize a custom mount. Stresses and strains in the elastomer cross-section for the new optimized mount were compared to the original design. The new, optimized design had a 40% reduction in strain while maintaining the same overall height as the current design (Figure 2).
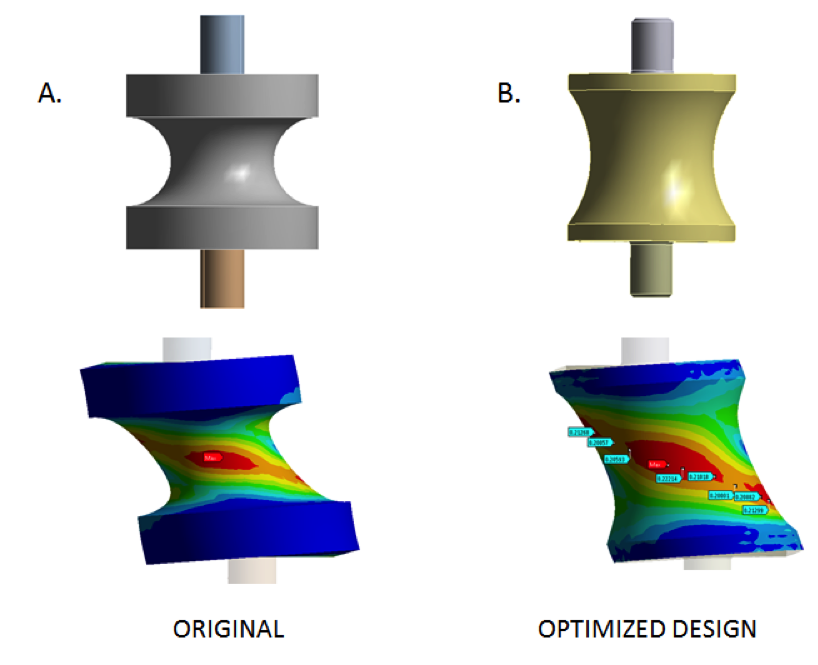
Figure 2 – Original (A) versus optimized design (B). The optimized design had a 40% reduction in shear strain for improved durability.
The custom mount was then prototyped and tested to verify performance requirements were met.
Conclusion:
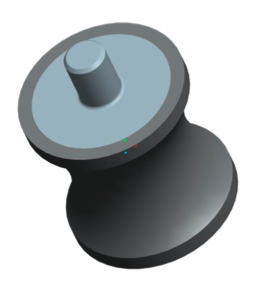
Figure 3 – Redesigned, optimized mount.
The redesigned, optimized mount (Figure 3) was successfully durability tested for 10,000 cycles and statically tested to verify stiffness requirements were met. The new optimized mount has performed successfully for nearly a decade.